La sovralimentazione in generale.
"Si
definisce sovralimentazione l'operazione mediante la quale si
precomprime l'intera (od una parte della) carica fresca al di fuori
del cilindro di lavoro, con lo scopo di aumentare la massa di aria o
miscela che un motore riesce ad aspirare per ogni ciclo" (G.
Ferrari, Motori a combustione interna). In pratica, mediante un
compressore, l'aria viene immessa nei cilindri ad una pressione
superiore a quella atmosferica; ciò permette che una maggiore
quantità di combustibile, proporzionale all'aumento di densità
dell'aria precompressa, possa
venir bruciata all'interno del cilindro. Come risultato si ottiene
un incremento della potenza specifica ed un miglioramento del rapporto peso/potenza di
un dato motore. Per comprendere meglio come la sovralimentazione
permetta di ottenere un aumento di potenza, si ricordi come per un
motore a quattro tempi (dove un ciclo completo viene compiuto con
due giri di manovella, corrispondenti a quattro corse del pistone)
la potenza utile effettiva (Pe) viene
definita dall'equazione 1, dove la pme è
la pressione media effettiva, V è la cilindrata unitaria, n
il numero di giri ed il 2 al denominatore rappresenta il numero di
giri dell'albero motore per avere un ciclo completo.
(equazione
1)
Dall'equazione
sopra riportata si nota come, a parità di cilindrata unitaria, due
siano le strade perseguibili per l'innalzamento della potenza: la
prima è innalzare il numero di giri, strada seguita dai motori
aspirati, con la conseguente
ricerca di un alleggerimento delle masse in moto per ridurre
l'inerzia; la seconda è incrementare la pressione media effettiva
ed è proprio quella seguita dai motori sovralimentati.
La pme è definita dall'equazione 2, dove h
è il rendimento del motore, l è il coefficiente di riempimento,
r la densità dell'aria,
Hi è
il
potere
calorifico superiore del carburante e a
è il rapporto aria/combustibile.
(equazione
2)
La
sovralimentazione permette di aumentare la densità dell'aria
(essendo la densità data dal rapporto massa/volume, ad un aumento
della massa si ha un aumento di r)
ed il coefficiente di riempimento (all'apertura della valvola di
aspirazione, i gas residui della combustione vengono compressi dalla
carica fresca che quindi può occupare un volume maggiore con un
conseguente miglioramento di l):
di conseguenza sia la pressione media effettiva che la potenza utile
effettiva si accrescono. La
sovralimentazione presenta anche altri vantaggi, quali il
miglioramento del rendimento del motore (attraverso un miglioramento
del processo di combustione), cosa ancora più evidente nei motori
Diesel, in cui si riesce a ridurre il ritardo di accensione, la
riduzione delle emissioni di particolato ed una combustione più
graduale che permette di avere un motore dal funzionamento più
silenzioso. Tra gli svantaggi si ha un aumento dei carichi
meccanici (determinato dalla
maggiore pme) e termici. Inoltre, per i
motori ad accensione comandata, si verifica la detonazione con il
conseguente "battito in testa": ciò perché una parte
della miscela si trova in condizione di autoaccendersi ancor prima
di essere raggiunta dal fronte di fiamma regolare. Proprio per
ridurre questi inconvenienti,
i motori sovralimentati presentano un rapporto di compressione
inferiore a quello degli aspirati. La riduzione del rapporto dì
compressione determina la riduzione dei picchi di pressione e delle
temperature massime sviluppate durante la combustione entro i limiti
tollerati dal motore, consentendo di aumentare pressioni e
temperature medie effettive del ciclo. In tal modo si ottengono
aumenti di potenza, coppia e carichi meccanici medi, mentre si
diminuiscono le punte di carico massimo sugli organi in movimento. Ora
che qualche elemento teorico è stato chiarito, ci si può chiedere:
come realizzare la sovralimentazione? I due metodi più
utilizzati sono il compressore volumetrico ed il turbocompressore,
mentre un terzo, il Comprex, non viene utilizzato.
Il
compressore volumetrico. Il compressore volumetrico (fig. 1) è
costituito da due lobi che comprimono l'aria all'aspirazione; esso
viene azionato direttamente dal motore tramite una trasmissione a
cinghia o a catena.
Il
vantaggio principale di tale soluzione è che, essendo il
compressore centrifugo, azionato dal motore, la sovralimentazione è
attiva già a basso
numero di giri: per
questo motivo tale soluzione ha conosciuto una certa diffusione nei
rally. Lo svantaggio principale di tale soluzione è l'assorbimento
di potenza ai danni del motore.
Il
turbocompressore. Particolare
attenzione deve essere soprattutto rivolta al metodo più utilizzato
per ottenere la sovralimentazione, il turbocompressore (fig. 2). Il rotore della turbina, messo in rotazione dai
gas di scarico che gli cedono parte della loro energia, trascina
(mediante un albero poggiante su due supporti antifrizione
lubrificati dall'olio motore) la girante (in alluminio) del
compressore che comprime l'aria aspirata.
L'aria
compressa in uscita dalla girante del compressore ha una temperatura
di più di 80°: per questo motivo l'aria compressa, prima di essere
immessa nel motore, viene raffreddata per mezzo di uno scambiatore
di calore aria/aria, altrimenti detto intercooler (fig.
3). I vantaggi della post-refrigerazione, in termini di potenza,
sono quantificabili
empiricamente:
una diminuzione di 10 °C crea un aumento del volume dell'aria pari al 3%, a cui corrisponde un incremento di potenza pari
al 3,5%.
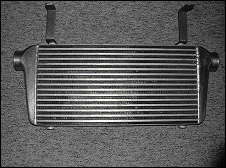
|
Un
turbocompressore, durante il funzionamento, raggiunge velocità di
rotazione molto elevate, dai 60.000 ai 180.000 giri/min; per questa
ragione, bisogna prestare particolare cura alle condizioni dell'olio motore (con i relativi filtri), che ha il compito di
lubrificarne e raffreddarne gli elementi. Anche per tale motivo, in
alcuni casi viene utilizzato uno scambiatore di calore per l'olio.
La pressione di sovralimentazione, che in alcune applicazioni supera
il bar, viene regolata tramite una valvola waste-gate
(fig. 4), una valvola di sfiato che impedisce una eccessiva pressione di
sovralimentazione riducendo la quantità dei gas di scarico diretti
alla turbina. La waste-gate, che può essere a piattello o a
saracinesca, è azionata da un piccolo polmone comandato
pneumaticamente e collegato allo scarico del compressore da un tubo di piccole
dimensioni.
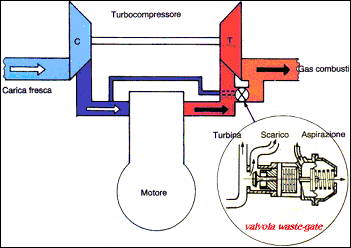
|
La
valvola si apre quando la pressione a valle del compressore supera
il valore predefinito da progetto: questo fa sì che il piccolo
polmone vada ad agire, tramite un'asta, sulla molla della waste-gate,
vincendone la resistenza in modo da aprire la comunicazione diretta
con i gas di scarico, bypassando così la turbina. Variando il
precarico della molla si può variare la pressione massima di
sovralimentazione. Esiste in alcuni motori la possibilità di
ritardare l'intervento della waste-gate, in modo da disporre per
brevi periodi di un plus di potenza grazie all'aumento della
pressione oltre il valore massimo prestabilito. Questo sistema,
chiamato overboost, mediante un attuatore comandato da
una centralina elettronica, agisce direttamente sulla waste-gate.
Nei motori diesel, una possibilità di regolazione della
pressione di sovralimentazione è fornita da una turbina a
geometria variabile (fig. 5). In pratica, il distributore
della turbina, cioè l’elemento che convoglia i gas di scarico
verso il rotore (girante), è dotato di palette che tramite un meccanismo ad aria
compressa variano la loro
inclinazione
in funzione del regime di rotazione del motore.
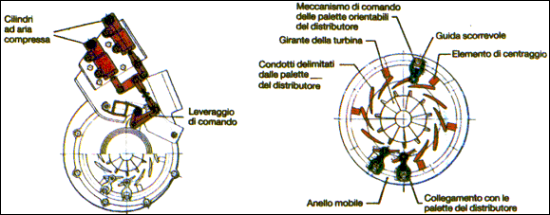
|
Questo
permette di avere un controllo delle sezioni di passaggio dei gas di
scarico e, di conseguenza, un controllo dei gradi di
sovralimentazione ottenibili ai diversi regimi. L'utilizzo di questa
soluzione è limitato ai motori diesel perché la temperatura dei
loro gas di scarico è inferiore rispetto ai motori a benzina: ciò
permette condizioni di utilizzo meno gravose per i delicati
componenti di tale soluzione. La turbina a geometria variabile
permette anche di attenuare uno dei problemi più importanti dell'applicazione
di un turbocompressore, il cosiddetto turbo lag, cioè il
ritardo di risposta in accelerazione del turbo. In passato, questo
problema era molto sentito, rendendo le auto sovralimentate
difficili da guidare: ciò perché, al di sotto di un determinato
regime (ad esempio, sotto i 3000 giri/min), il flusso dei gas non
era sufficiente per mettere in rotazione la girante del turbo e
quindi non bastava a garantire una pressione di sovralimentazione
adeguata; di conseguenza, il motore aveva un funzionamento simile a
quello di un motore aspirato con un rapporto di compressione basso e
quindi con una risposta fiacca. Superato tale regime, la sovralimentazione
diventava invece molto evidente e
difficile da gestire. Questo problema si attenua nei diesel, anche
per la loro caratteristica tipica di avere molta coppia già ad un
ridotto numero di giri. Nei motori a benzina, invece, il problema è
accentuato dal fatto che, in fase di rilascio, la turbina,
anche se priva della spinta indotta dai gas di scarico, a causa
della propria inerzia continua a girare velocemente causando un
aumento di pressione indesiderato nel collettore di aspirazione che
in rilascio è chiuso dalla farfalla. Per evitare che la valvola a
farfalla venga danneggiata viene utilizzata una valvola by-pass,
grazie alla quale l'aria viene convogliata, tramite un tubo, a valle
del filtro dell'aria in maniera silenziosa, in modo da mantenere
comunque elevata la pressione di esercizio e da non far fermare del
tutto il compressore anche ad acceleratore chiuso. Nelle vetture da
competizione viene invece utilizzata la cosiddetta valvola pop-off
che devìa verso l'esterno l'aria in pressione, producendo il sibilo
in fase di rilascio tipico dei motori turbo da gara. In qualsiasi
caso, ad una riapertura della valvola a farfalla il compressore deve
essere riportato a regime con un conseguente ritardo del
raggiungimento della pressione di sovralimentazione. La risoluzione del
turbo lag,
per i motori a ciclo Otto, è stata ottenuta in vari modi. Una
strada seguita è quella di ridurre la dimensione della turbina e,
di conseguenza, del rotore/girante: ciò permette di ridurne la
massa e quindi anche l'inerzia, in modo che i gas di scarico
riescano a metterla in rotazione più velocemente riducendo i tempi
di risposta ai comandi dell'acceleratore e garantendo che la
pressione di sovralimentazione venga raggiunta più rapidamente.
Un'altra strada è la bassa sovralimentazione che migliora il
rendimento del motore rinunciando a picchi elevati di potenza,
permettendo di mantenere un rapporto di compressione vicino a quello
di un aspirato e, quindi, garantendo una elasticità di
funzionamento del motore anche a turbina quasi o del tutto ferma. In
conclusione si può affermare che la sovralimentazione è diventata
ormai parte integrante dei motori a ciclo Diesel, ma che
probabilmente si assisterà ad un suo utilizzo massiccio anche nei
motori a ciclo Otto, al fine di migliorarne il rendimento e ridurne
le emissioni inquinanti.
Materiale
tratto da AUTOTECNICA
aprile 2004
|